The 3-phase brushless DC motor has an operating voltage of 72V, rated power of 3.8 kW, rated speed of 3000 rpm, rated current of 62A, and rated torque of 12 Nm. 72V 600W brushless DC motor works more efficiently with a matching controller/gearbox.
Basic Specifications
Model: BLDC-180WDM12030
Matched Controller Model: KBL
Rated Power: 3.8 kW
Rated Voltage: 72V
Rated Current: 62A
Phase: 3 phase
Holding Torque: 12 Nm
Max. Torque: 30 Nm
Rated Speed: 3000 rpm
No-load Speed: 3600 rpm
Square Flange Size: 180 mm
Working Efficiency: 85%
Insulation Grade: F
Protection Grade: IP65
Motor Lead Length: 30 cm, if buy a kit (motor+controller), an extra 1 meter of wire shall be provided.
Certificate: CE, RoHS, ISO
Weight: 18.6 kg
Note: Power, Voltage, Speed, Shaft, Motor Length, and Motor Lead of BLDC Motors can be customized.
Features
- Stable speed control: 72V brushless motor continues to set speed and a feedback signal is compared from the speed of the motor to adjust the voltage applied to the motor; therefore, even if the load change, still can set the speed from slow instantaneous adjustment to, and in order to stabilize the running speed.
- Thin, high power: 3 phase DC motor adopts a permanent magnet brushless motor rotor, thus realizing the thin and high power.
- Wide speed control range: 3800W brushless DC motor speed control range than speed ac motor and inverter wider, because unlike the speed ac motor that at low speed have restrictions on the use of torque, so there is no brush motor is suitable for from low speed to high speed, all require the use of a certain torque.
- Contribute to energy saving: The rotor of the brushless dc electric motor is used for the permanent magnet, which can reduce the two-loss of the rotor, so the power consumption is reduced by more than 20% compared with the three-phase induction motor with variable frequency control, which is helpful for the energy saving of the device.
- Equipped with protection function: 72V 3.8 kW BLDC motor can help to protect the safety of the equipment system.
Dimension (Unit: mm)
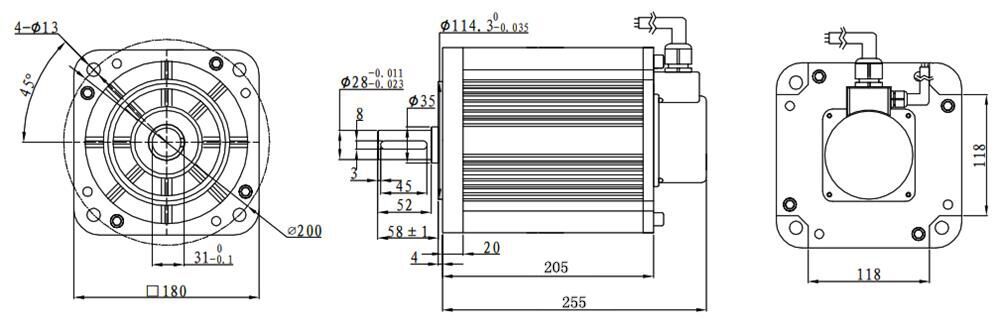
Line Define
Power Wire
Red |
Yellow |
Blue |
Motor U |
Motor V |
Motor W |
Feedback Wire
Hall Line Color |
Hall Signal Definition |
Plug Serial Number |
Orange and Black |
5V |
1 |
Orange |
0V |
2 |
Yellow |
Hall A |
3 |
Blue |
Hall B |
4 |
Green |
Hall C |
5 |
Speed - Torque Curve
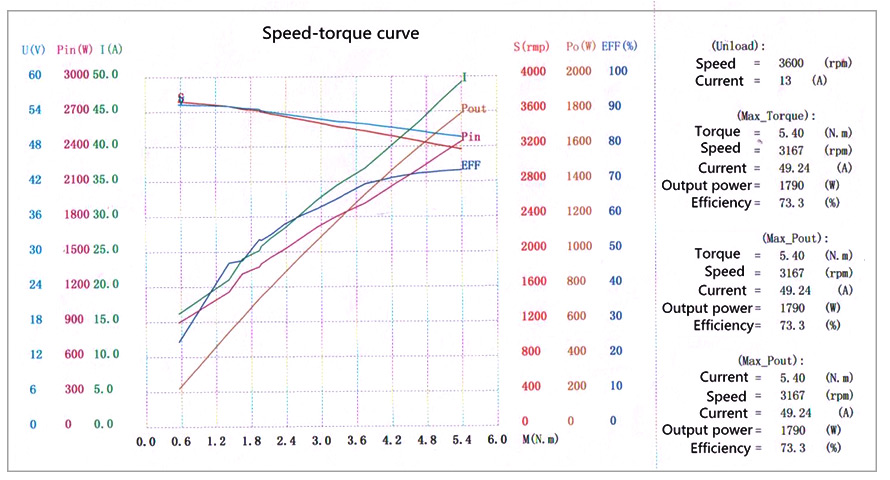
Details
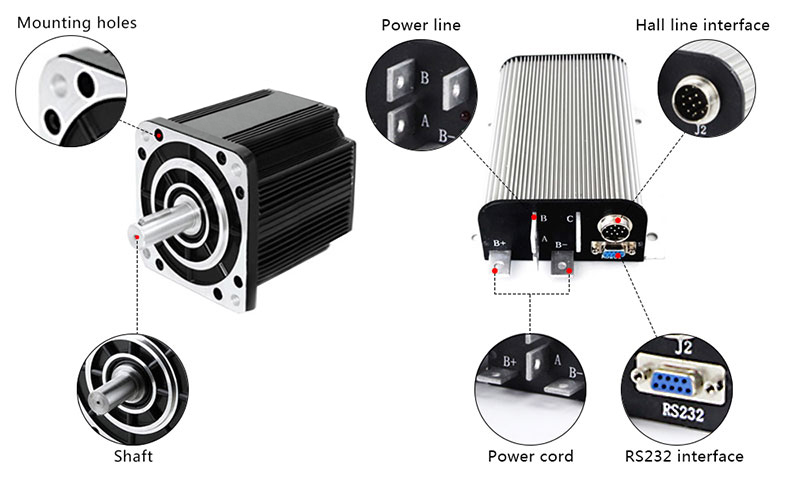
Applications
96V 3800W Brushless DC motors are widely used in our lives, such as electric bicycles, inverter air conditioners, washing machines, drones, automobiles, CNC machine tools, polishing and grinding equipment, packaging machinery, tools, turnstiles, industrial control, medical machinery, automation to, AGV trolley, aerospace, and intelligent storage equipment, etc.
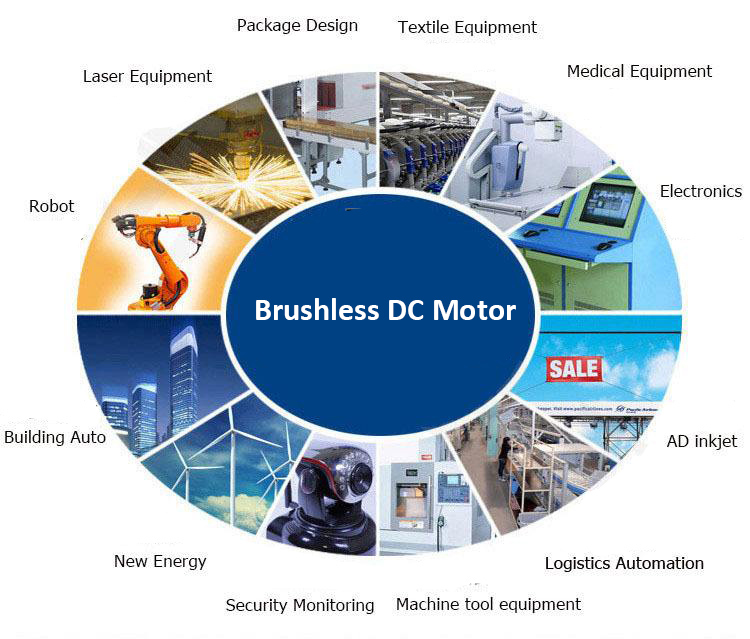
Tips: Is it possible to drive a BLDC motor with a sine wave instead of a square wave?
To drive a BLDC motor, you do need drive electronics to "find" the rotor position and match the line frequency to the speed and accelerate to the desired speed. For low-speed, high-load motors, Hall effect sensors are typically used to determine the rotor position directly. At higher speeds, it is possible and more effective to use the drive coil itself for counter-electromotive force detection. (For motors started at minimum load, for example, driving a model airplane propeller, the start-up algorithm can open-loop accelerate the motor to the speed at which counter-electromotive force detection begins to operate, although this is not entirely reliable.)